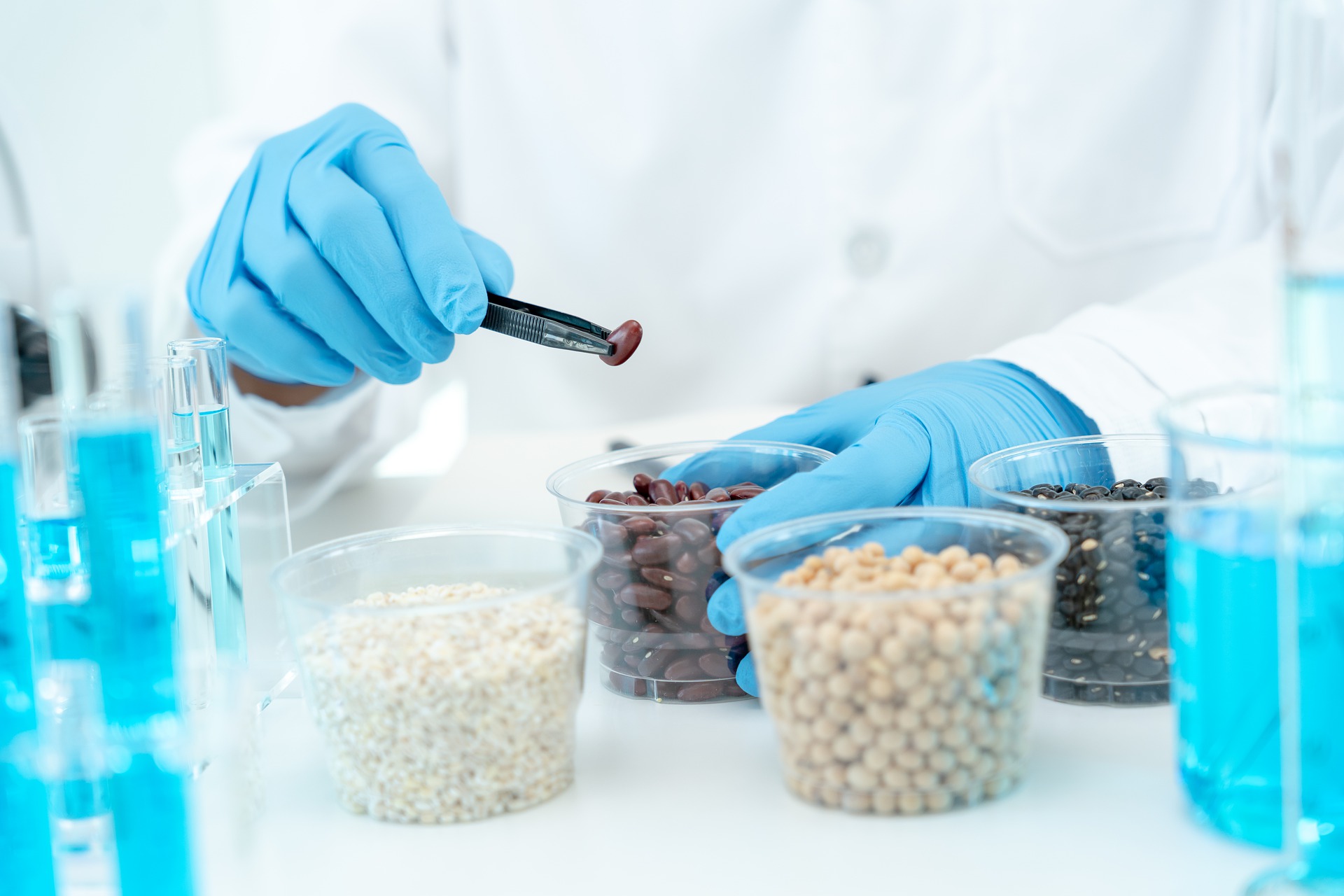
Learn everything you need to know about process validation in this comprehensive guide. Understand the importance of this critical process and how to implement it effectively to ensure product quality and regulatory compliance.
Process validation is an essential component of any manufacturing process. It involves establishing documented evidence to ensure that a process consistently produces products meeting predetermined specifications and quality attributes. This crucial step in the production cycle helps to guarantee safe, efficacious, and high-quality products for consumers.
In this comprehensive guide, we will delve into the ins and outs of process validation, including its purpose, regulatory requirements, and steps involved. We will also explore the various types of process validation and the importance of establishing a robust validation program. So, whether you are new to process validation or looking to enhance your current practices, this guide has got you covered. Let’s jump in!
Purpose of Process Validation
The primary purpose of process validation is to ensure that a manufacturing process consistently produces products meeting predetermined specifications and quality attributes. This includes verifying that the process can consistently meet regulatory requirements, such as GMP (Good Manufacturing Practices), and produce safe, efficacious, and high-quality products for consumers.
Process validation also helps companies identify potential sources of variability in their processes and implement measures to control and eliminate them. For instance, process validation at Polarseal helps businesses identify and mitigate any risks to product quality, safety, or efficacy. It is to ensure that products consistently meet customer expectations and comply with regulatory standards throughout their lifecycle.
Regulatory Requirements for Process Validation
Process validation is a mandatory requirement for pharmaceutical and medical device companies to comply with regulatory standards. In the United States, the Food and Drug Administration (FDA) requires manufacturers to validate their processes in accordance with Current Good Manufacturing Practices (cGMP). Similarly, the European Medicines Agency (EMA) has also issued guidelines for process validation in Europe.
These regulations aim to ensure that all products undergo a rigorous and standardized validation process to guarantee their safety, quality, and efficacy. Companies must adhere to these requirements to avoid regulatory action and maintain consumer trust in their products.
Steps Involved in Process Validation
Process validation typically involves three phases: process design, process qualification, and continued process verification. During the process design phase, companies develop a detailed understanding of their process and identify critical control points. In the process qualification phase, they demonstrate that their process can consistently produce quality products within predetermined specifications.
Once the initial validation is complete, companies must conduct ongoing monitoring and testing to ensure that the process remains in a state of control. This is known as continued process verification and involves regular audits, reviews, and evaluation of data to maintain product quality.
Types of Process Validation
There are three types of process validation: prospective, concurrent, and retrospective. Prospective validation is performed before the start of commercial production and involves establishing documented evidence that a process can consistently produce products meeting predetermined specifications.
Concurrent validation is conducted during routine production to verify that the process remains in a state of control. This type of validation ensures that any changes or modifications do not affect product quality. Retrospective validation involves reviewing historical data to confirm that a process has consistently met predetermined specifications.
Each type of validation serves a unique purpose and is essential in maintaining the reliability and consistency of the manufacturing process.
Importance of Establishing a Robust Validation Program
Establishing a robust validation program is crucial for ensuring the safety, efficacy, and quality of products. It helps companies identify potential sources of variability in their processes and implement measures to control and eliminate them. This leads to consistent production of high-quality products that meet customer expectations and comply with regulatory standards.
A robust validation program also allows for continuous improvement, as ongoing monitoring and data analysis can identify areas for optimization. This not only ensures a reliable manufacturing process but also results in cost savings and improved efficiency. Companies with a strong validation program are better equipped to handle unexpected issues and maintain consumer trust in their products.
Role in Ensuring Safe, Efficacious, and High-Quality Products
The ultimate goal of process validation is to ensure the production of safe, efficacious, and high-quality products for consumers. By verifying that a process consistently meets predetermined specifications and regulatory requirements, companies can guarantee the safety of their products.
Process validation also plays a critical role in ensuring product efficacy by identifying and controlling potential sources of variability that may affect product performance. For instance, it helps to ensure that the correct amount of active ingredient is present in each dose of a medication. Additionally, it helps maintain consistent quality throughout the production process, leading to reliable and satisfactory products for consumers.
Potential Consequences of Not Implementing Proper Process Validation
Not implementing proper process validation can have severe consequences for companies, including product recalls, regulatory actions, and damage to brand reputation. Without a robust validation program, there is no guarantee that products will consistently meet quality standards, potentially jeopardizing consumer safety.
Improper process validation can also result in costly product failures and delays in production. In the pharmaceutical industry, a lack of proper validation has led to medication shortages and disruptions in patient care. Companies must prioritize process validation to avoid these consequences and maintain the integrity of their products.
Continuous Improvement and Ongoing Monitoring as Part of Process Validation
Process validation is an ongoing process that requires continuous improvement and monitoring to maintain a state of control. By regularly reviewing data and conducting audits, companies can identify areas for optimization and implement changes to improve their processes.
Ongoing monitoring also helps companies detect any potential issues or variations in the manufacturing process, allowing for timely intervention and maintenance of product quality. It is an essential aspect of process validation, as it ensures that the established processes continue to produce safe, efficacious, and high-quality products throughout their lifecycle.
Process validation is a critical aspect of the manufacturing process that ensures safe, efficacious, and high-quality products for consumers. It involves establishing documented evidence to guarantee that processes consistently meet predetermined specifications and regulatory requirements. By following the steps involved in process validation and implementing a robust validation program, companies can maintain product quality, prevent recalls and regulatory actions, and continuously improve their processes. It is essential for companies to prioritize process validation to ensure the reliability and consistency of their products, ultimately leading to consumer confidence and satisfaction.
Was this news helpful?