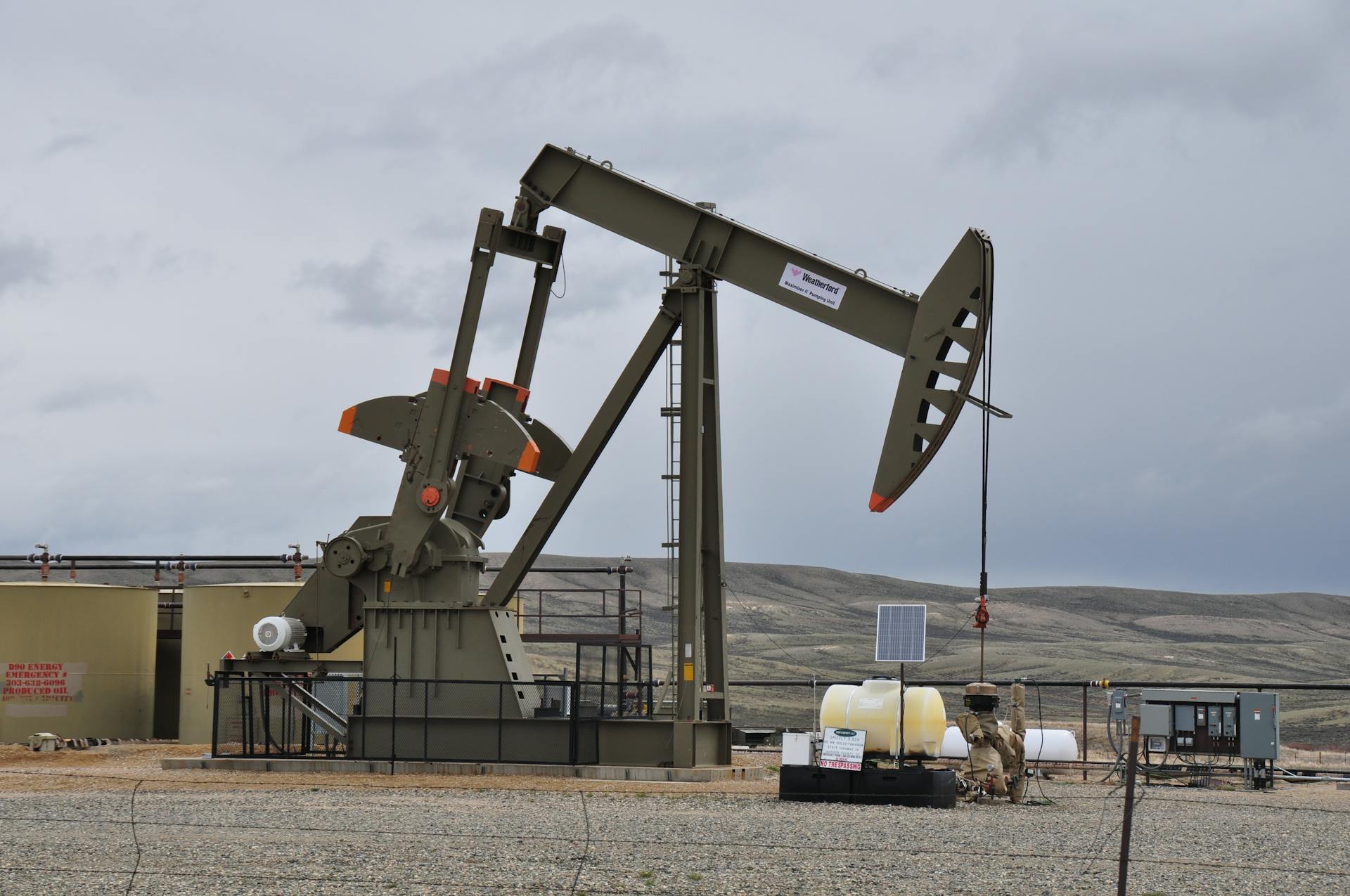
Discover how advanced pumping solutions support critical operations across industries like oil and gas, pharmaceuticals, food processing, mining, and more. Learn about the role of reliable pump systems in enhancing efficiency, safety, and sustainability while meeting industry-specific demands in today’s complex and evolving industrial landscape.
The role of pumping systems in the industries goes far beyond merely moving fluids from one point to another. These solutions are vital cogs in the operational machinery of countless sectors, including oil and gas, pharmaceuticals, food processing, water treatment, mining, and many more. Efficient and reliable pumping solutions ensure the smooth flow of liquids, slurries, chemicals, and even gases under varying pressures and temperatures.
As technology evolves and industries become more complex, the demand for tailored, high-performance pump systems grows significantly. Companies depend on these systems for productivity and environmental compliance, worker safety, and energy efficiency. In this article, we’ll explore how pumping solutions support vital operations across multiple industries, examining their design, application, benefits, and future trends.
Meeting the Demands of the Oil and Gas Industry
The oil and gas sector relies heavily on robust pumping systems to manage everything from crude extraction to refined product distribution. Pumps are critical in drilling operations, chemical injection, and pipeline transportation. These pumps must withstand harsh conditions, including corrosive fluids, high pressures, and extreme temperatures. Centrifugal and positive displacement pumps are commonly used, with advanced sealing systems and materials that ensure durability. Downtime in this industry can lead to massive financial losses and safety hazards, making reliable pump performance a top priority. Innovative pumping solutions that include remote monitoring and predictive maintenance features are now being adopted to reduce operational risks and improve efficiency.
Powering Operations in the Mining Sector
Mining operations are among the most demanding industrial environments, requiring equipment that can endure abrasive slurries, extreme depths, and unpredictable conditions. From dewatering flooded shafts to transporting mineral-rich slurries, pumps are indispensable to maintaining continuous production. In surface and underground mining, reliable pump equipment plays a central role in minimizing downtime and managing operational risks. These systems must perform consistently despite being exposed to corrosive chemicals, heavy particulates, and fluctuating loads. Innovations such as variable speed drives, automated monitoring, and energy-efficient motors are increasingly being implemented to enhance performance and reduce environmental impact. By optimizing fluid handling processes, mining operations can improve safety, productivity, and cost-effectiveness in even the harshest terrain.
Providing Critical Support in the HVAC Industry
Heating, ventilation, and air conditioning (HVAC) systems depend on pumps to circulate water, refrigerants, and other fluids that regulate indoor climates in commercial and residential buildings. Circulator pumps, booster pumps, and condensate pumps are vital for maintaining temperature control and energy efficiency. With growing demand for smart building solutions, today’s pumping systems are increasingly equipped with sensors and IoT connectivity, enabling predictive maintenance and automatic adjustments to optimize performance. High-efficiency pumps that meet standards such as those outlined by the U.S. Department of Energy (DOE) are now widely used to reduce energy consumption and operational costs in large-scale HVAC applications.
Ensuring Sanitation and Accuracy in the Pharmaceutical Sector
In pharmaceutical manufacturing, precision and hygiene are paramount. Pumps used in this industry must meet stringent regulatory standards, such as those set by the FDA and cGMP. Sanitary pumps, including diaphragm and peristaltic models, are commonly used for dosing, transferring, and filling processes. These pumps are designed for easy cleaning and sterilization to prevent contamination. The materials used must be chemically inert and compatible with sensitive compounds. In this high-stakes environment, a single pump failure can compromise entire batches of products. Pharmaceutical companies depend on high-accuracy, contamination-free pumping systems that are often integrated with automated process controls.
Enhancing Productivity in the Food and Beverage Industry
The food and beverage industry demands pumping solutions that can handle a wide range of products, from thick pastes to carbonated liquids, without altering their quality or consistency. Pumps used here must adhere to food safety standards, like those outlined by the EHEDG or 3-A Sanitary Standards. Hygienic lobe, peristaltic, and diaphragm pumps are frequently employed due to their gentle handling and ease of cleaning. These pumps support critical operations like blending, metering, and bottling. To meet the growing demand for high-speed, high-volume production, the latest systems include smart sensors and control technologies that allow real-time adjustments, minimizing waste and enhancing output.
Supporting Water and Wastewater Treatment Systems
Effective water and wastewater management is vital for public health, environmental protection, and industrial operations. Pumping systems are central to these processes, enabling the transportation of clean water to consumers and the movement of wastewater to treatment facilities. Submersible pumps, centrifugal pumps, and progressive cavity pumps are widely used for various stages, from influent handling to sludge dewatering. With increasing emphasis on sustainability, modern pumping solutions are engineered for energy efficiency and low maintenance. Advanced control panels and monitoring systems help optimize pump performance, reduce energy consumption, and extend service life, contributing to greener infrastructure.
Driving Efficiency in the Chemical Processing Industry
Chemical plants face unique challenges that demand specialized pumping systems capable of handling highly corrosive, abrasive, and hazardous materials. Precision, reliability, and leak prevention are critical factors in selecting the right pump. Magnetic drive pumps, gear pumps, and diaphragm pumps are commonly used due to their ability to safely manage volatile fluids without seal failures. Material compatibility is crucial, with many systems incorporating PTFE, Hastelloy, or other specialized materials to resist chemical degradation. With safety and compliance at the forefront, these industries are increasingly adopting double containment systems and advanced monitoring technologies to detect leaks and prevent accidents.
Supporting Critical Operations in the Marine Industry
Marine applications require pumping solutions for bilge systems, ballast control, fuel handling, and waste management. Pumps in this industry must be rugged, compact, and capable of operating in corrosive saltwater environments. Marine pumps are often made from specialized alloys or polymer composites to resist corrosion and ensure long-term performance. Redundancy and ease of maintenance are key considerations given the difficulty of repairs at sea. Innovations such as remotely monitored systems and self-priming pumps have significantly improved operational efficiency and reliability in maritime operations, ensuring that vessels stay compliant with international safety and environmental regulations.
Fueling Efficiency in Agricultural Irrigation Systems
Agriculture depends on efficient pumping systems to deliver water to crops and livestock, particularly in regions where rainfall is unpredictable. Pumps used in irrigation must handle varying water qualities, including those with sediment or high salinity. Common pump types include centrifugal, submersible, and turbine pumps. With water conservation becoming a pressing concern, modern agricultural systems incorporate technologies like drip irrigation and VFDs to deliver precise water volumes, reduce waste, and lower energy costs. These systems contribute to improved crop yields and more sustainable farming practices, helping feed growing populations while preserving natural resources.
Boosting Safety in Fire Protection Systems
Fire protection systems in industrial, commercial, and residential buildings depend on high-performance pumps to deliver water or foam rapidly and efficiently during emergencies. These systems are critical in suppressing fires and minimizing damage, requiring pumps that are durable, responsive, and capable of operating under extreme conditions. Fire pumps must adhere to rigorous standards such as NFPA 20, ensuring they are tested for reliability and performance. Typically driven by diesel engines or electric motors, they are built for immediate activation and continuous operation throughout fire events. Common types include jockey pumps for maintaining pressure, vertical turbine pumps for deep water sources, and split-case pumps for high-volume demands. Integration with fire alarms, control panels, and backup power supplies ensures comprehensive system readiness, enhancing safety and compliance.
Strengthening the Role of Pumps in Renewable Energy
As the world transitions to renewable energy, pumping solutions play a crucial role in technologies like geothermal systems, solar thermal plants, and biofuel processing. In geothermal energy, pumps circulate heat-transfer fluids between underground reservoirs and surface systems. Solar thermal systems use pumps to move heated fluids to storage tanks or distribution systems. In biofuel production, pumps handle viscous organic materials during conversion processes. The challenge lies in ensuring that these systems are energy-efficient and capable of long-term, low-maintenance operation. Continued innovation in pump design and materials will support the broader adoption of renewable energy technologies worldwide.
Enabling Flexibility in Industrial Manufacturing
In general industrial manufacturing, pumps are used for coolant circulation, lubrication, cleaning processes, and hydraulic power. Each application may require different specifications in terms of flow rate, pressure, chemical compatibility, and temperature resistance. Industrial manufacturers benefit from customizable pumping solutions that offer flexibility, modularity, and automation compatibility. As competition intensifies and product quality becomes paramount, manufacturers turn to smart pumps to integrate with Industry 4.0 platforms. These advanced systems provide real-time diagnostics, automated alerts, and remote control, helping operators make data-driven decisions that minimize downtime and maximize productivity across production lines.
Pumping solutions are foundational to the successful and safe operation of virtually every major industry. From the precision needed in pharmaceuticals to the rugged reliability required in mining, these systems are customized to meet diverse operational demands. As industries face increasing pressure to become more sustainable, efficient, and resilient, the evolution of pumping technology is critical. Innovations such as smart sensors, IoT integration, energy-efficient designs, and corrosion-resistant materials are shaping the future of industrial pumps. By investing in the right pumping systems, businesses can enhance productivity, ensure safety, and maintain compliance while navigating the challenges of a dynamic global economy.
Was this news helpful?