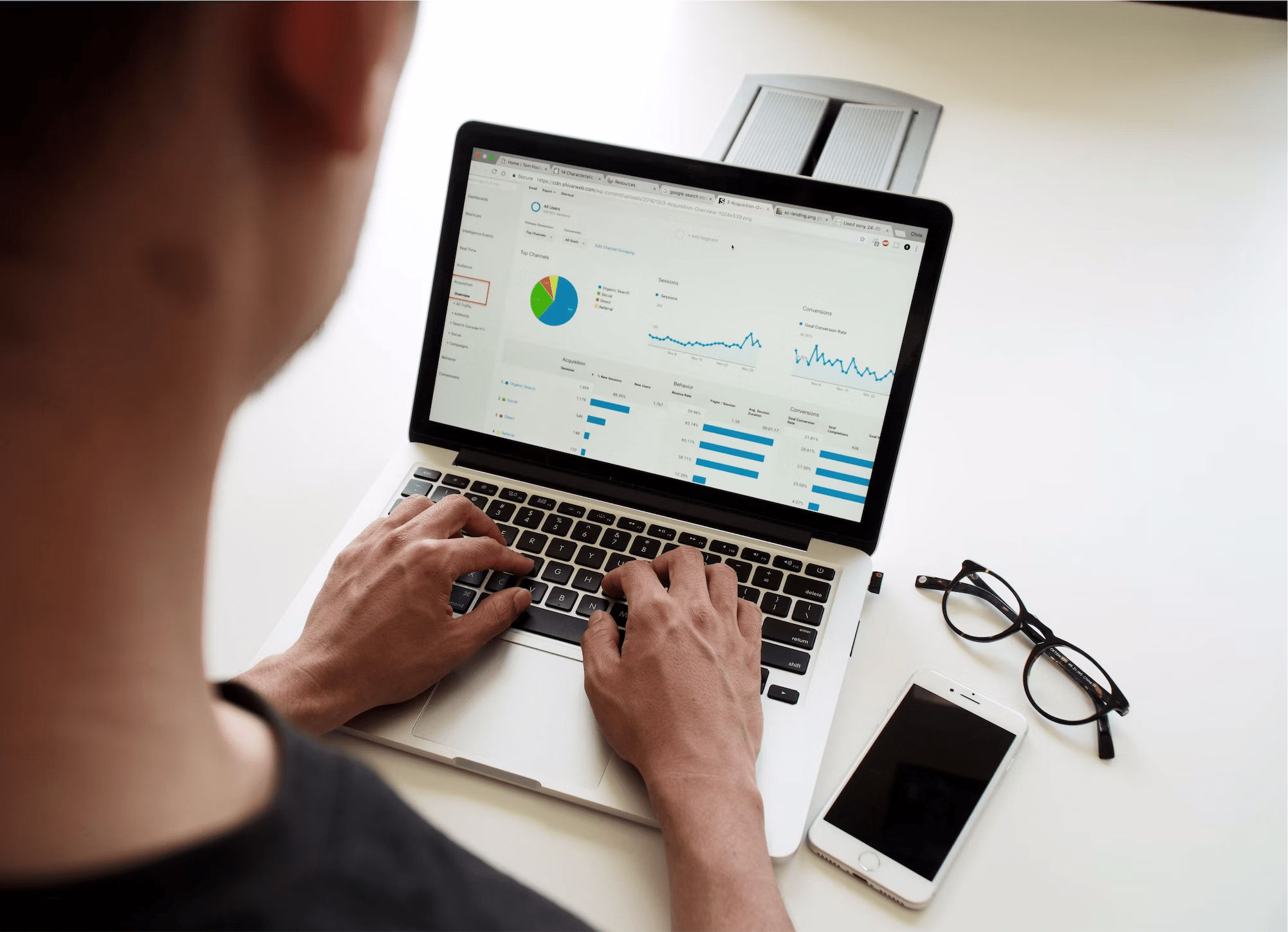
Elevate your manufacturing processes with cutting-edge data analytics solutions. Uncover the power of real-time monitoring, predictive analytics, and advanced data insights. Learn how manufacturing data, sourced from machines and human factors, enhances quality control and efficiency. Explore the role of data analytics in optimizing operations, reducing costs, and boosting profitability. Discover the types of data generated in manufacturing and implement data analytics platforms for seamless analysis. Power your business intelligence with Microsoft Power BI through experienced consultants. Embrace a data-driven approach to streamline processes, cut costs, and elevate productivity. Overcome challenges with effective advanced analytics, providing a complete view of your business data for informed decision-making. Transform your manufacturing future with data-driven efficiency and competitiveness.
Manufacturing processes are complex and highly sensitive to fluctuations in supply chains, market trends, and other factors. Today’s manufacturers need real-time data analytics solutions that can help them optimize their operations and reduce costs across the board. Implementing advanced data analytics provides invaluable insights into various facets of the manufacturing workflow, enhancing efficiency, and enabling proactive decision-making. By leveraging predictive maintenance, quality assurance, and analytical models, manufacturers can not only streamline their processes but also elevate the overall standards of productivity and quality. The integration of data analytics platforms ensures a seamless aggregation of data from diverse sources, offering a comprehensive view that empowers businesses to stay competitive and agile in the dynamic manufacturing landscape.
What is Manufacturing Data?
Manufacturing data is a dynamic amalgamation of information derived from various sensors and sources. This real-time data is not limited to manufacturing facilities but extends to diverse industrial locations. The multifaceted nature of manufacturing data renders it instrumental for predictive maintenance, ensuring machinery operates optimally. Quality assurance relies on this data to uphold stringent standards, identifying potential issues before they escalate. Moreover, predictive analytics harnesses the power of manufacturing data, facilitating ongoing process optimization. By leveraging this comprehensive dataset, businesses gain valuable insights into operational nuances, paving the way for informed decision-making and continuous improvement initiatives. The continuous flow of real-time data from machinery and industrial processes establishes a foundation for efficiency, quality, and innovation.
The Role of Data Analytics in Manufacturing
Data analytics is a way of using data to make decisions. It’s a process that helps manufacturers improve processes and increase productivity. Data analytics can be used to improve efficiency, reduce costs, and increase profitability by improving quality control, reducing waste, or enhancing customer service.
To harness the full potential of data analytics, businesses often turn to powerbi consultants who specialize in leveraging Microsoft Power BI. These consultants provide expertise in implementing robust data analytics strategies, creating insightful visualizations, and extracting meaningful insights from complex datasets. By collaborating with experienced powerbi consultants, businesses can unlock the power of their data to drive informed decision-making and gain a competitive edge in the market.
Types of Data Generated in Manufacturing
Data in the manufacturing industry can be categorized into four types:
- Data from machines. This includes sensor data, operational data, and performance information. For example, a machine may have sensors that monitor its temperature or vibration level while it is in operation; this would be considered operational data since it’s specific to how this particular piece of equipment operates. Operational data also includes performance metrics such as yield rate or uptime percentage the amount of time that the machine was able to produce goods versus being down for maintenance or repair purposes.
- Data from people who work on or with these machines (for example, operators). These are typically referred to as “human” factors within an organization because they represent some aspect related directly to human interaction with systems used for manufacturing processes (like robots). Human factors include things like employee satisfaction surveys/questionnaires which could indicate satisfaction levels among workers using certain types of equipment over others; thus giving companies insight into whether there might need adjusting before making any major changes happen down the line. Also included here would be things like absenteeism rates among employees who regularly use certain pieces of machinery which could indicate safety concerns about working conditions at hand.
Implementing Data Analytics Platforms
Data analytics platforms are crucial tools for optimizing manufacturing processes. Comprising three main components, these platforms play a pivotal role in harnessing the power of data:
- Data Sources: The platform aggregates data from diverse sources, including IoT sensors and other relevant inputs.
- Advanced Analytical Models: Utilizing sophisticated analytical models, these platforms dissect the collected data, extracting valuable insights.
- User Interface: The user interface translates these insights into visually accessible formats, ensuring that even non-technical users, such as managers, can comprehend and leverage them for informed decision-making.
Integrating a reliable solution like business intelligence for manufacturing can empower your organization to streamline processes, cut costs, enhance efficiency, and boost overall productivity. Additionally, these platforms contribute to waste reduction and elevate the standards of quality assurance in manufacturing operations.
Real-time Monitoring and Predictive Analytics
The next step in the manufacturing process is real-time monitoring and predictive analytics. The goal of this step is to predict future events, such as machinery breakdowns or product defects so that you can prevent them from happening. For example, if a piece of equipment has been running for several hours without any problems, but then suddenly stops working for no apparent reason (and can’t be restarted). Then it’s likely there’s an issue that needs attention before it causes further damage or downtime.
To do this effectively requires access to large amounts of data including historical information about similar incidents that would otherwise be difficult (if not impossible) to obtain manually; however thanks to advances in technology over recent years we now have tools that make these tasks much easier than before!
Overcoming Challenges in Data Analytics Adoption
To overcome these challenges and make the most of your data, it’s important to understand how you can use advanced analytics effectively.
Data Analytics Platforms: A data analytics platform is a tool that allows users to access and analyze their data seamlessly. It should provide them with real-time monitoring capabilities so they can detect issues as they arise, as well as predictive analytics capabilities that allow them to predict future problems before they happen. This will allow them to react proactively instead of reactively when something goes wrong in production or another part of their business process.
A data analytics platform should also be able to provide users with a complete view of their business data so they can better understand how it works and make more informed decisions. This will help them avoid costly mistakes and improve their overall performance.
Data analytics is the future of manufacturing. With the right tools and strategies, you can make your organization more efficient and competitive by leveraging the power of data. By adopting a data-driven approach to managing your operations, you can reduce waste, improve quality control, and increase profitability while saving time and money on manual processes like reporting.
Was this news helpful?